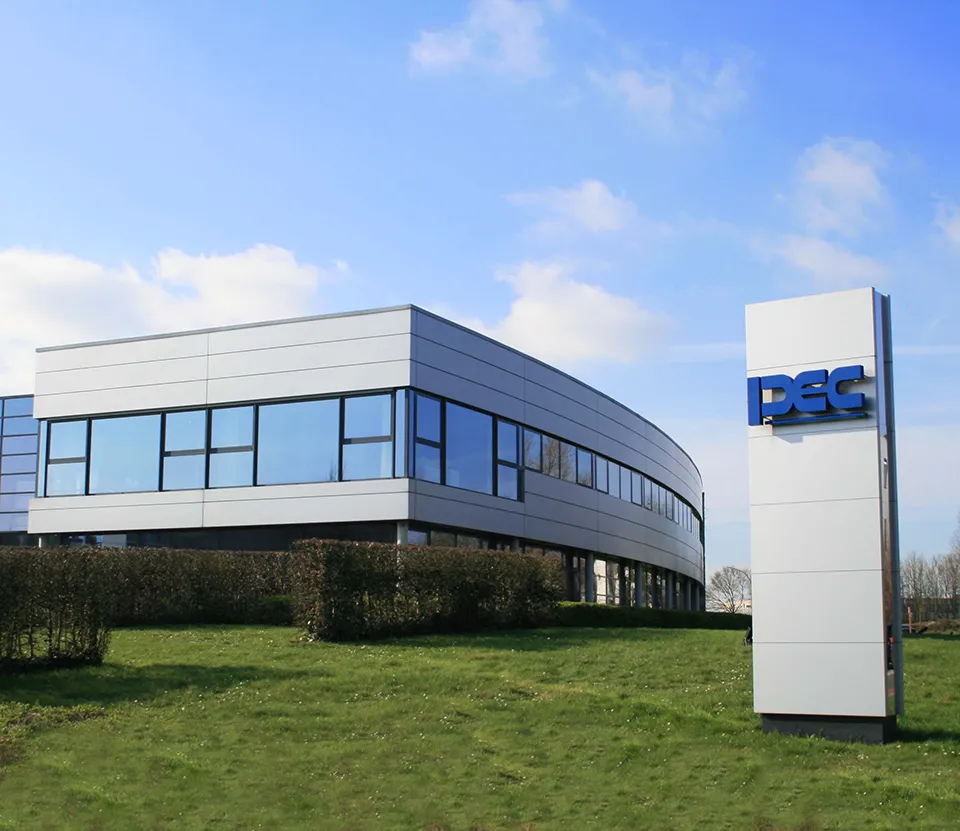
Experts
in battery cell
manufacturing
and testing
BUILDING THE CELL
GIGA FACTORIES
OF TOMORROW
PEC helps battery cell producers and OEMs in the development and scale up of their GIGA factories. We provide the technology and equipment for the complete cell activation including RAPID Single-Step Electrolyte Filling, soaking, charging, final degassing and sealing, formation, ageing and testing of battery cells with a clear focus to the Total Cost of Ownership. The PEC technology reduces energy consumption and improves cell performance and yield.
Testing Equipment for:
- R&D Labs
- QA Labs
Manufacturing Equipment for:
-
GIGA Factories
-
Pilot Lines
-
R&D Lines
ENABLING
HYBRID
CELL MANUFACTURING
Hybrid Cell manufacturing is decoupling Electrode production, Cell Assembly and Cell activation by supplier, location and time.
Hybrid Cell manufacturing enables battery related companies to focus to their core skills and business activities, creates cost reductions, removes technical barriers and reduces financial risks. Hybrid Cell Manufacturing is the (only) way to gradual ramp GIGA scale battery cell production in a cost-effective way.
Ιnnovation
At PEC, we believe innovation means more than just developing products and solutions. We work together with our clients to create new processes, to help them successfully step up volumes, quality and performance.
We strive in continuously searching for optimized manufacturing, testing and logistics processes. By always exploring new technologies and investing in them, we also create an environment where our employees can bring innovation to bear on every aspect of their jobs.
We are setting our sights beyond the borders of our industries by exploring new ways of working with an ecosystem of technology suppliers, business partners, universities and institutes. This innovation sets us and our customers apart from competition.
Our Story
The First years
Founded in 1984 in Leuven, Belgium, we began our journey with an automotive project for Alfred Teves Gmbh (ATE – now Continental). In 1984, ATE had just started the development of ABS braking systems for Ford. Unlike their competitor Bosch, ATE planned to make this game-changing technology available as standard for a mid-size car model and the broader public.
The ATE factory in Mechelen was set to produce the ABS sensors and valves for this very advanced product at the time. PEC was chosen to develop and build the test equipment for the ABS sensor part. However, this test equipment was very complicated, and the budget was limited.
1984 was a time when process computers were still very expensive, and PLCs hardly existed. Being creative, we decided to use one of the very first Commodore PET personal computers and could get our hands on an additional I/O board that was developed by SCK Mol for the Nuclear industry. All design work was still very manual, the mechanics were made in small workshops, and everything was assembled in Luc’s garage, where I developed the controls and software – all in low-level assembly language, there simply was nothing else.
Both the Ford Scorpio and the ABS system became massive successes, where PEC did a great job and secured the order for a full-scale automated multimillion (BEF) test line. New employees joined the company and the development of several new innovations, such as a very accurate optical positioning system and a cable shielding tester, were realized. PEC was on its way…
In 1985, the Ford Scorpio was introduced to the European market with a Teves electronic system throughout the range as standard. For this, the model was awarded the coveted European Car of the Year Award in 1986, with very favorable praise from motoring journalists. After this success, Ford began research into Anti-Lock systems for the rest of their range, which encouraged other manufacturers to follow suit… (Wikipedia)
The IBM years
In 1985, one year after our first projects, IBM launched its 7532: the first 19” industrial PC that was not only rugged and 19” rack-mounted, but also had several slots that allowed us to plug in commercially available and self-developed interface cards – a big plus and a perfect upgrade for our control strategy; exactly what we needed.
After a very challenging accreditation process, PEC got approved and became a certified IBM System Integrator. IBM further expanded its manufacturing offerings with control boards, software, and even industrial robots.
Robotics were still mysterious and uncommon when PEC installed the very first flexible and intelligent manufacturing cells at Volvo Car and VYNCKIER (GEC). These innovative projects were covered in the press, garnering full attention for PEC.
The combination of advanced IBM hardware and software, with PEC as an innovative system integrator, was clearly a winning formula. The relationship was upgraded to a point where IBM invested 30% in PEC’s capital.
PEC became a preferred system integrator for IBM Shop Floor applications in EMEA. Many innovative industry projects for the most demanding customers were successfully completed, not only in automotive but also in other industries and companies such as Philips, ASML, BAT, GTE, and many others.
Our references were picked up by the IBM development team in Boca Raton (Florida) and PEC was invited to present its projects during the annual IBM Manufacturing Technology Days in Fort Lauderdale. Around 500 executives from leading global manufacturing companies attended the event.
Covering the latest innovations in battery manufacturing we implemented with Duracell Batteries, we received the desired attention. During a coffee break, I was suddenly surrounded by a team of Koreans who wanted to start producing the first Li-Ion Cells (18650) outside Japan. One month later, we received a large delegation from Samsung in Belgium and started the next chapter in our History.
Entering the Battery business
Automotive Cells
Building Giga Factories
Our future roadmap
Management
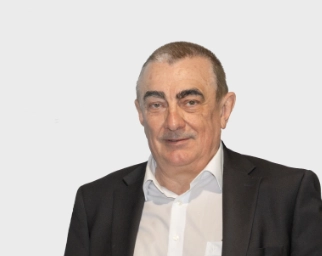
Raf Goossens
CEO & Founder
Chairman of the Board
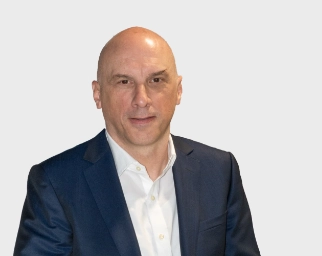
Peter Ulrix
Vice President, Sales & Marketing
Executive Board Member
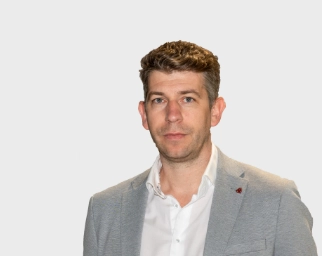
Stef Leemans
Vice President, Product & Proposal Management
Executive Board Member
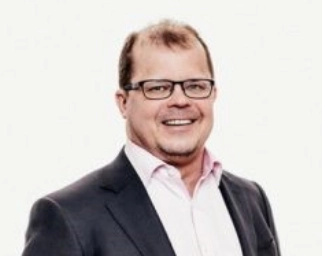
Dr. Tech Mika Räsänen, PhD.
Non-Executive Board Member
Locations
Tatabánya
PEC Central Europe Kft.
Táncsics Mihály út 2/C, 2800 TATABANYA, HUNGARY
Budapest
PEC Central Europe Kft.
Lánchíd u. 23. V/2 H-1013 BUDAPEST, HUNGARY
Tel: +36 1- 487-70-10
Leuven
PEC NV.
Researchpark Haasrode 1839, Technologielaan 12, B- 3001 Leuven
Telephone: +32(0)16/39.83.39
Coconut Creek
PEC North America Inc.
4911 Lyons Technology Parkway #1
Coconut Creek, Florida 33073, USA
Tel : +1 (561)-962-2824
Boca Raton
PEC North America Inc.
2385 NW Executive Center Drive Suite 100,
Boca Raton FL,33431, USA
Tel : +1 (561)-962-2824
Ariake
PEC Japan kk.
Level 9, Ariake Frontier Building Tower B, 3-7-26 Ariake, Koto-ku, TOKYO 135-0063 JAPAN
〒135-0063 東京都江東区有明三丁目7番26号 有明フロンティアビルB棟9階
Tel: +81 3 5530 9326
Tokyo
PEC Japan kk.
Legend Loran floor 1 1-2-7, Haginaka, Ota-ku, TOKYO 144 0047, JAPAN
〒144 0047 東京都大田区萩中1-2-7 レジェンドローラン1階
Gersthofen
PEC Germany GmbH.
Senefelderstraße 15, 86368 Gersthofen, GERMANY
Huzhou
PEC Test and Manufacturing Equipment (Huzhou) Co., Ltd.
Room 101, building 3, No 299 Zijing Road,
Wuxing District, Huzhou 313000, Zhejiang Province, CHINA
Tel: +86 (0)57 2210 2950
湖州工厂:
浙江湖州市紫荆路299号3幢101室,邮编 313000
Pulau Pinang
PEC South East Asia Sdn. Bhd.
No.1609 & 1610, Jalan Nafiri,
14100 Simpang Ampat,
Pulau Pinang.
Malaysia