Cell Filling and Finishing Lines for 46XXX Cylindrical Cells
Our lines include all process steps including Rapid Single Step electrolyte filling, soaking, pre-charging, degassing, formation, final sealing, ageing, testing and final inspection and packaging
Cell Filling and Finishing Lines for Hard-Case Prismatic Cells
Our lines include all process steps including Rapid Single Step electrolyte filling, soaking, pre-charging, degassing, formation, final sealing, ageing, testing and final inspection and packaging
Cell Finishing Lines for Pouch Cells
Our lines include all process steps including soaking, roll-pressing, formation, degassing, ageing, testing and final inspection and packaging.
Cell Filling and Finishing Lines for 21700 Cylindrical Cells
Our lines include all process steps including soaking, formation, ageing, testing and final inspection and packaging
Total Cost of Ownership in Li-ION Cell Finishing
High volume Li-ION cell production is powering today’s wearable electronics and will be the key to success in the electrification of our daily mobility. Li-ION Giga-factories require fully automated and vertically integrated processes with minimum Work-In-Process and material handling.
PEC covers all cell manufacturing technologies from electrolyte filling to final testing and sorting of the cell. This manufacturing stage is referred to as Cell Finishing and performs the complete Cell Activation.
The equipment is positioned on both sides of an Automated Storage and Retrieval System (ASRS). The ASRS crane system will automatically transport the cells from one process step to the next until all process steps are finished.
The unique PEC concept helps cell manufacturers in significantly optimizing their Total Cost of Ownership (TCO) by reducing costs and improving cell quality and yield.
Rapid Single-Step Electrolyte Filling
Today, Electrolyte filling is one of the key process challenges in GIGA-scale, hardcase Li-ION cell production. With increasing cell energy densities, the path to full wetting of the electrodes is very time-consuming and adds significant complexity to the production process.
In response to these challenges, PEC has developed a unique Rapid Single-step Electrolyte Filling solution with several patents pending. It significantly reduces the electrolyte filling time (filling and soaking) from hours to minutes. It further eliminates the need for multiple filling steps, while achieving an absolute higher state of wetting without any cell modifications.
The technology not only has a direct impact on CAPEX and OPEX for cell manufacturers, but also improves yield. Additionally, improved cell performance is observed because of the higher wetting state of the cells before formation.
PEC has already implemented this leading technology in several GIGA-scale manufacturing plants. The process is ideally suited for large format cells, such as the 46XXX cylindrical cells as well as prismatic cells. To avoid complex logistics between the Formation, Ageing & Testing lines and the dry room area, PEC’s new electrolyte filling machine has been fully integrated into the PEC Automated Cell Finishing Lines.
Scalability from 100’s of MWh to GIGA scale Production
PEC’s turn-key single line approach simplifies the complexity of Cell Finishing and provides the required modularity to scale up your factory form 100’s of MWh to GIGA scale production.
The Automated Cell Finishing Lines are designed for fully automatic operation. PEC believes that automation during all stages of production is essential in achieving consistent quality and throughput at competitive manufacturing costs.
This guarantees a cost-effective operation in all geographies and is the only way for cell and battery suppliers to move away from the pilot production stage and establish a reliable high volume supply chain for a HEV, PHEV or EV car assembly plant.
Manufacturing Safety
The cell finishing process forms the biggest risk factor in Li-ION factories. During this production stage the cells will be activated and will reach their rated capacity after several charge and discharge cycles. Individual performance will be checked against specifications using high C-rate pulses on the cells.
During this process any cell or equipment related imperfection may lead to electrolyte fires, gas explosions and even worse a thermal runaway of a cell. Examples of these events are well known in the industry. Therefore, safety is PEC’s main concern in the design and continuous improvement of the automated cell finishing lines.
The key point of PEC’s safety design is prevention. The lines are equipped with a very long list of safety related techniques and features to prevent thermal runaway from happening.
On top PEC’s unique formation station design offers a completely passive safety enclosure for any electrical process on the cells. In case of a thermal runaway of a cell the formation station protects the other cells and stations from propagation due to the fire and gas explosions.
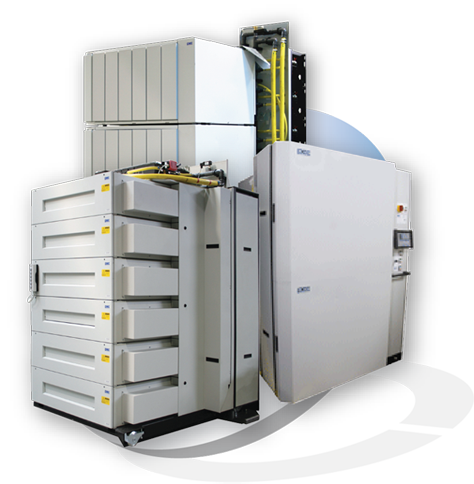